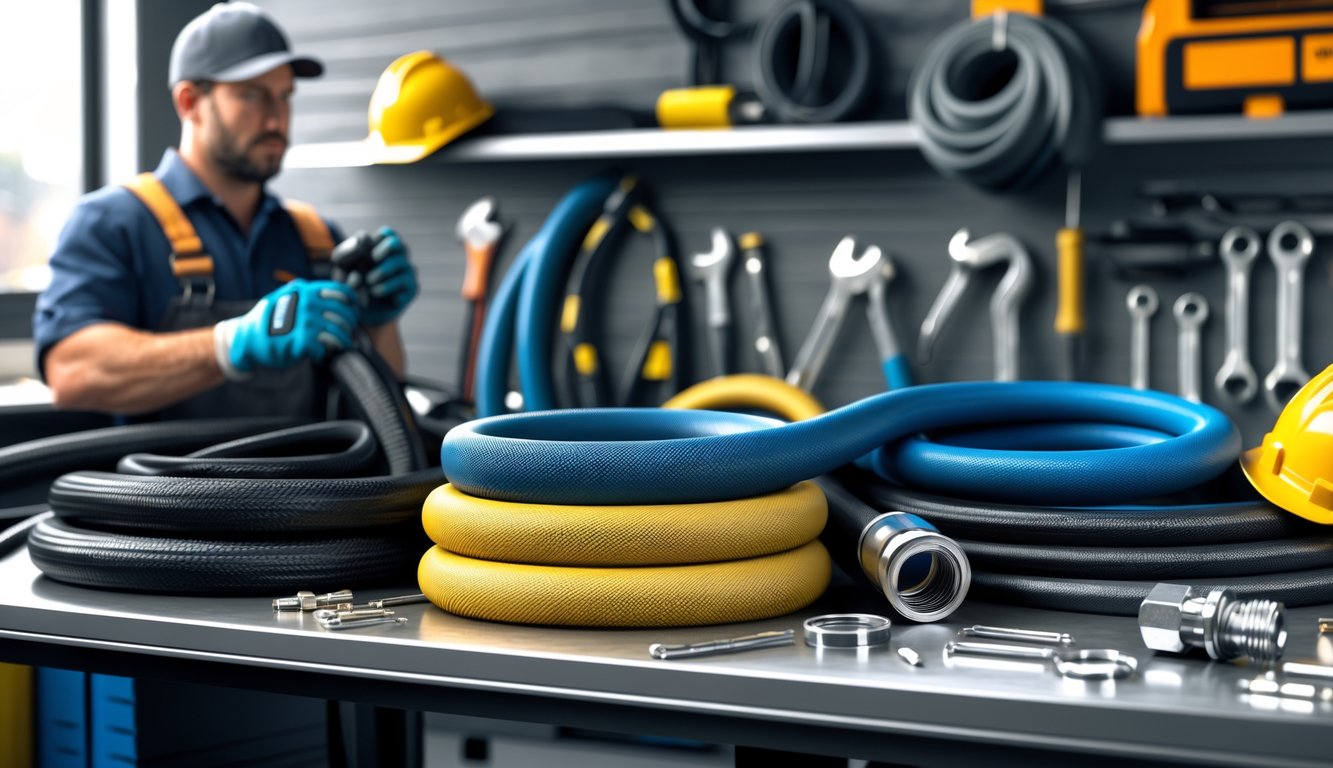
Comparing Popular Contractor-Approved Brands
Here’s what I don’t get—why does Flexzilla stain my hands, but I still use it? Contractors drop brand names like they’re trade secrets, but everyone just wants a hose that won’t embarrass them in front of clients. Specs matter more than marketing, and these brands actually show up on jobsites (and in shop rants, and sometimes in curses when someone runs one over).
Flexzilla Hose Performance
Five minutes in and I’m already untangling a neon green Flexzilla hose. It’s like wrestling a python. But—no kinks, no memory. Watched a crew tie one in a knot, water kept flowing. Reviewers on This Old House love it, even after it gets run over.
Weather? Doesn’t care. Some hoses turn into bricks below 40°F, but Flexzilla’s still bendy in the teens. No clue why it leaves that weird residue on my hands, but whatever. The 50-footer’s about 8 pounds—not light, but not a backbreaker. Even old-school irrigation guys admit it outlasts vinyl by years. Only real downside: lime green is loud. Maybe too loud for fancy yards.
Bionic Steel Hose Longevity
Ever seen someone drag a Bionic Steel hose behind a truck? I have. Didn’t break. You’d think steel mesh would kink, but nope. “Never rust, never burst”—yeah, don’t believe everything, but it’s tough. It’ll flatten a bit under high pressure, which matters if you run fancy nozzles or splitters.
I left mine out all winter in New England. Snow, ice, whatever. Still worked in spring—though the couplings loosened up after a few deep freezes. Weight’s weird: 50 feet feels heavier when you’re coiling it, but lighter than the old rubber monsters. Some contractors say it’s not great for soft landscaping, but for concrete work, it’s a must. Unless you lose it under a pile of scrap, which—yeah, happens.
Eley Hose and Hoselink Reliability
So here’s the thing: I’ve dragged an Eley hose around a truck tire, over concrete, through a mess of rebar—still tight, still threading like it just left the factory, those brass fittings refusing to mangle even when I’m careless. There’s this 10-year warranty they can’t stop bragging about at trade shows—contractors love to one-up each other with horror stories about other hoses dying in two seasons. Eley’s not trying to win any beauty contests; it’s the near-indestructible materials that matter. You can abuse it and the seams don’t split. That’s honestly rare.
Hoselink—yeah, that’s the one with the all-in-one quick connect thing. I watched a plumber get so sidetracked demoing those snap-on nozzles he forgot his actual job for half an hour. He swore off regular fittings forever. It’s not perfect, though; the Australian threads are a pain for US setups, so you end up hunting for adapters. Still, both Eley and Hoselink have this weird underground rep—guys literally mark their hoses so nobody “accidentally” walks off with them. Me? Three years in, haven’t snapped an Eley fitting, but I’ve managed to break basically everything else with threads. Maybe that’s a me problem.
Key Performance Characteristics
Every year there’s someone convinced they’ve figured out the “secret” to the best hose—until they drag it across pea gravel or wrap it around a brick wall in January and, surprise, it falls apart. Most hoses can’t take real-world abuse. You want something that doesn’t collapse at the first kink and can handle actual job sites, not just whatever the box promises.
Water Pressure and Burst Rating
Honestly, I used to ignore burst ratings. “Who cares? I don’t run my sprinklers that long.” Joke’s on me. Cheap hoses split if a washer clogs or the spigot gets bumped. Burst pressure isn’t just a number for nerds—300 PSI or more is what you want, and that’s not overkill. TCH Industries even says, “choosing the right material…withstand the temperatures your hose will see is the difference between a hose that lasts years, or…” and then it gets all doom-and-gloom.
Thermoplastic hoses? Usually can’t match rubber for pressure. Rubber hoses stick around for 5–10 years, thermoplastics maybe 3–7. Contractors keep mental notes: flexible, reinforced, real brass, not that “crush-resistant” plastic nonsense. They check spec sheets, not Amazon reviews—nobody wants to explain a burst hose to the boss.
Weather Resistance for Year-Round Use
I’ve seen hoses turn brittle and weirdly colored after one cold snap. Try explaining UV resistance to a neighbor who thinks blue hoses are just for looks. Material matters: synthetic rubber survives sun, vinyl gets cooked, polyethylene shatters if it freezes. Hose material guides spell it out—rubber’s good for cold, polyurethane laughs at heat, but wind up a frozen PVC hose and, snap, you get two hoses.
Some contractors swear up and down that their composite blend will “never decay.” I mean, that can’t be true, but whatever. It’s not just about resistance—it’s about the hose snapping back after heat or frost. Weatherproofing isn’t magic, but that blue stripe on pro hoses? Sometimes it actually means something—if it’s certified, like ASTM D471. If not, it’s just more paint.
Crush-Proof Couplings and Fittings
If you haven’t flattened a hose fitting under a truck tire yet, just wait. “Crush-proof” is slapped on every box, but most fail at the couplings. I switched to brass after ripping off a plastic fitting with pliers before sunrise one morning. Real commercial brass lasts for ages, as long as the gaskets aren’t garbage. The knurling actually helps when your hands are wet.
Some estimator at Anaconda Pipe and Hose once told me, “Your hose is only as strong as your crimp.” He’s right—a split at the neck ruins your day. Flex-sealed or swaged assemblies can take a beating, but not a full-on roll-over. If you care about numbers, check for crush resistance ratings (if you can even find them). And don’t assume “stainless steel” means anything—Chinese stainless isn’t the same as US or EU stuff, and every plumber I know will go on a rant about it.
Flexible Garden Hose Technology
Flexible hose ads never mention what happens after six months when the hose “remembers” every kink and now just snakes all over the place. Real flexibility isn’t just about smooth coiling—it’s about layered construction (sometimes three-ply, sometimes five) with polyester or aramid fiber sandwiched in there. That matters because a limp hose stores flat but still holds pressure without ballooning. You only care when you trip over it in July.
Newer hoses use thermoplastic elastomers or hybrid rubbers—“kink-free,” supposedly. Ask anyone: none are truly immune if you coil them wet and toss them in a box. Contractors who hate swapping hoses every month are buying premium flexible ones with “no-lead brass connectors, reinforced outer mesh”—not for status, just to avoid fighting with memory recoil or unscrewing the ends constantly. “Lightweight expandable” hoses? Don’t. Unless you like buying new hoses every summer.